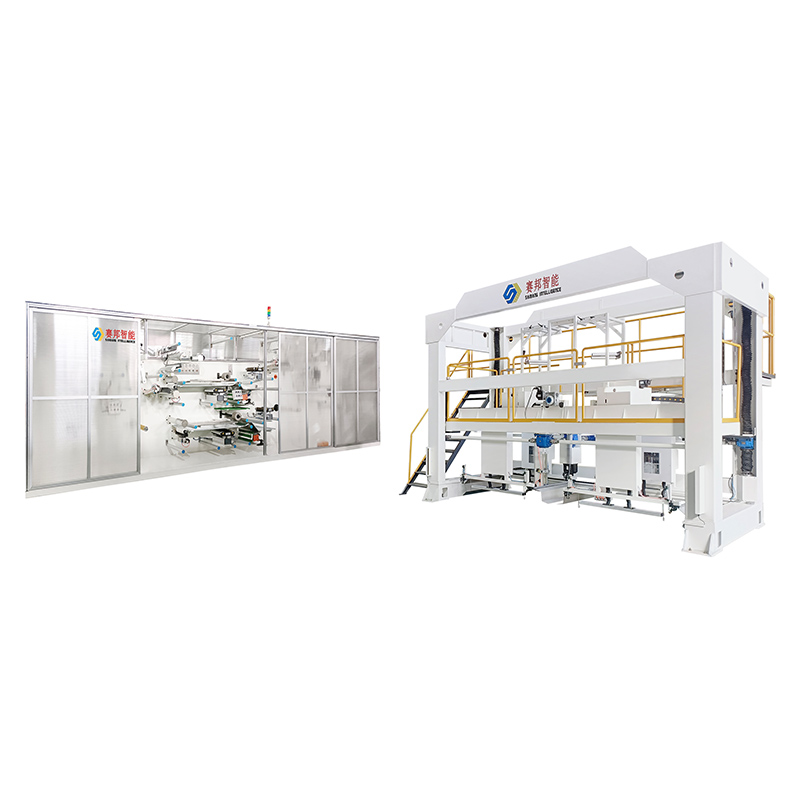
Automatic Sanitary Napkin Making Machine for Folding
Sanitary Pad Making Machine
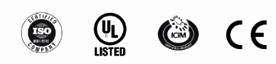
-
saya.ethan88@gmail.com Email
Automatic Sanitary Napkin Making Machine is an integrated and automated sanitary napkin production solution. This equipment integrates multifunctional modules such as wrapping, folding, stacking and dust removal, and realizes the continuous production of sanitary napkin core materials through a double-station automatic unwinding and material splicing system. Its core advantage lies in the high-precision full servo control system, which ensures that every link from material unwinding, compounding to finished product stacking has extremely high accuracy and stability, providing an efficient, intelligent and reliable production platform for the sanitary product manufacturing industry.
Automatic Sanitary Napkin Making Machine for Folding parameters
Model: | ZDBF-13B |
Brand: | Saibang Intelligence |
Adaptation Materials: | SAP Sheet,nonwoven. |
SAP Sheet Width: | 85-120mm |
Effective Width For C-Folding Material: | 135-260mm |
Max Design Speed: | 300m/min |
Normal Working Speed: | 180-250m/min |
Max C-Folding Speed: | 180-250m/min |
SAP Sheet Unwinding Diameter: | Φ1200mm |
OEM: | OEM/ODM |
Factory Nature: | China Manufacturers Suppliers Factory |
Automatic Sanitary Napkin Making Machine for Folding features
High-speed production system: The Automatic Sanitary Napkin Making Machine has a production speed range of 180-250 meters per minute, and a maximum design speed of 300 meters per minute. This high-speed production capacity is due to its advanced mechanical transmission system and optimized production process layout. For example, when producing a standard-sized sanitary napkin, the machine can stably produce about 12,000 finished products per hour, which greatly meets the needs of large-scale production and significantly reduces unit production costs. Its production efficiency is 40%-50% higher than that of traditional equipment, providing strong support for manufacturers in the fierce market competition.
Precise material adaptation system: The Automatic Sanitary Napkin Making Machine can accurately adapt raw materials with a width of 85-120 mm for SAP fiber sheets and an effective width of 135-260 mm for C-folded materials. This precise material adaptation capability ensures that various specifications of sanitary product core materials can be efficiently processed on the machine. At the same time, the equipment can support the unwinding diameter of SAP fiber sheets up to Φ1200 mm, which fully meets the requirements for the use of large-size raw materials, reduces the frequency of material changes during the production process, and further improves the overall production efficiency.
Dual-station automatic unwinding and material splicing system: Equipped with an advanced dual-station automatic unwinding and material splicing system, it can realize automatic material splicing and material change without stopping the production process. When the material of one unwinding station is about to run out, the other station can quickly take over to ensure the continuity of the production process. Actual application data shows that the system can reduce production interruption time by about 80%, greatly improving the utilization rate of equipment. In the 24-hour uninterrupted production mode, its effective production time is increased by nearly 2 hours compared with traditional single-station equipment, providing a strong guarantee for the company's efficient production.
Full servo control system: The whole machine adopts a full servo system to achieve precise control of each production link. The various actuators driven by the servo motor, such as unwinding, traction, folding, stacking, etc., all have high response speed and high control accuracy. According to the data provided by the equipment manufacturer, its control accuracy can reach ±0.1 mm, ensuring the dimensional stability and quality consistency of the product. At the same time, the full servo system has good dynamic performance, can quickly adapt to changes in production speed and process parameters, and ensure the stable operation of the equipment under different working conditions.
Precise folding and wrapping system: The folding and wrapping module of the automatic sanitary napkin machine adopts a high-precision mechanical structure and advanced control algorithm, which can ensure that the sanitary products are folded uniformly and wrapped tightly and accurately. After strict quality inspection, its folding accuracy can reach ±0.2 mm, and the wrapping qualified rate is as high as 99.8%. This precise processing effect not only improves the appearance quality of the product, but also enhances the product's performance, such as preventing leakage of contents, etc., providing consumers with a better product experience.
Efficient stacking and sorting system: The Automatic Sanitary Napkin Making Machine has an efficient stacking system that can neatly stack the finished sanitary products produced into a specified stack shape. During the stacking process, the equipment uses high-precision position sensors and stable mechanical transmission to ensure that each piece of product is placed accurately. According to actual production verification, its stacking neatness can reach ±0.3 mm, and the stacking speed is perfectly matched with the production speed, which effectively improves the efficiency of back-end packaging and warehousing. At the same time, the finished product after stacking is neat and stable, which is convenient for subsequent transportation and storage.
Dust removal and cleaning system integration: The automatic sanitary napkin machine has a built-in complete dust removal and cleaning system, which can remove dust, fiber debris and other impurities on the surface of raw materials and finished products in real time during the production process. With the use of efficient dust filtering devices and airflow control systems, its dust removal efficiency can reach more than 95%. This not only effectively improves the production environment, reduces the impact of dust on the precision parts of the equipment, and extends the service life of the equipment, but also improves the cleanliness of the product, meeting the high standards for the production of sanitary products.
Intelligent human-computer interaction system: The automatic sanitary napkin machine is equipped with an intuitive and easy-to-use intelligent human-computer interaction interface. Operators can easily set and adjust various production parameters such as production speed, material width, folding method, etc. through the touch screen or control panel. The system displays the operating status, production data and fault alarm information of the equipment in real time, which is convenient for operators to grasp the production situation in time and perform corresponding operations. According to user feedback, the learning curve of the human-computer interaction interface is short, and new employees can become proficient in operation after a brief training, which significantly improves production management efficiency.
Mass production of sanitary napkins: In the mass production of sanitary napkins, the Automatic Sanitary Napkin Making Machine can achieve continuous production of high-quality sanitary napkins at a low cost with its high-speed production capacity and the precision of the full servo control system. Its production speed of 180-250 meters per minute, combined with high-precision folding and wrapping functions, ensures the dimensional stability and quality consistency of the product. For example, when producing a standard-sized sanitary napkin, the equipment can stably produce about 12,000 finished products per hour, greatly improving production efficiency and meeting the needs of mass production. At the same time, the intelligent human-machine interface of the equipment enables operators to easily monitor and adjust production parameters to ensure the stability of the production process and the reliability of product quality.
Personalized sanitary product customization: With the increase in consumers' demand for personalized sanitary products, this automatic sanitary napkin machine has shown unique advantages in the field of customized production. Its flexible material adaptability and precise control system can meet the customization needs of sanitary products of different specifications and functions. For example, the equipment can accurately adapt to raw materials with a SAP fiber sheet width of 85-120 mm and an effective width of 135-260 mm for C-folded materials, supporting the production of sanitary napkin products of various sizes and liquid absorption performance. By adjusting the production parameters, the equipment can easily realize the personalized customization of products, meet the needs of specific consumer groups, and create higher added value for manufacturers.
New material research and development test: In the process of research and development of new materials for sanitary products, the equipment provides an ideal experimental platform for scientific researchers. Its stable production performance and precise control capabilities can ensure the accuracy and reliability of test data. For example, when studying the application of new SAP materials, the high-precision metering system of the equipment can accurately control the amount of SAP applied to ensure the repeatability and comparability of test results. Through the actual operation data of the equipment, R&D personnel can have a deeper understanding of the performance of new materials in the production process, providing a scientific basis for subsequent large-scale promotion and application.
Medical and health product production: In the field of medical and health care, the automatic sanitary napkin machine can be used to produce sanitary products that meet medical standards, such as sterile pads for surgery, wound care dressings, etc. Its efficient dust removal and cleaning system and precise folding and wrapping functions can ensure the sterility and safety of the products. For example, the dust removal efficiency of the equipment can reach more than 95%, effectively removing dust, fiber debris and other impurities on the surface of raw materials and finished products to ensure the cleanliness of the products. At the same time, the full servo control system of the equipment can accurately control every link in the production process to ensure the quality stability and reliability of medical supplies.
Emergency health material reserves: In response to natural disasters, public health incidents and other emergencies, the equipment can be quickly put into production to provide strong support for emergency health material reserves. Its high-speed production capacity and reliable operating performance can produce a large number of sanitary products in a short time to meet emergency needs. For example, in public health emergencies, the equipment can adjust the production plan in a short time, quickly produce sanitary napkin products that meet emergency needs, ensure the timely supply of emergency materials, and provide important guarantees for epidemic prevention and control and emergency rescue work.
Automatic Sanitary Napkin Making Machine for Folding maintenance
Daily cleaning and maintenance: In order to ensure the normal operation of the equipment and extend its service life, a comprehensive cleaning is required after the daily production. First, turn off the power of the equipment and use compressed air to blow away dust, paper scraps and other debris on the surface and corners of the equipment to prevent their accumulation from affecting the accuracy and performance of the equipment. Then, use a soft damp cloth dipped in a small amount of neutral detergent to gently wipe the outer surface, control panel and operating handle of the equipment to remove oil and fingerprints. For key components such as conveyor belts, rollers and cutting devices inside the equipment, special cleaning tools are required for detailed cleaning to remove residual glue, fiber and SAP powder to ensure smooth material transportation and processing. After cleaning, wipe all parts with a clean dry cloth to avoid moisture residue causing rust on the equipment or short circuit of electrical components. Regular daily cleaning can effectively reduce the equipment failure rate and maintain the efficient operation of the equipment, which can generally extend the service life of the equipment by 3-5 years.
Regularly check the wear of key components: Key components of the automatic sanitary napkin machine such as unwind shafts, winding shafts, tension sensors, metering pumps and cutting tools will gradually wear out during long-term use, affecting production accuracy and efficiency. It is recommended to conduct a detailed inspection of these components once a week. When inspecting, first turn off the equipment and cut off the power supply, carefully observe the surface wear of each component, and check whether there are scratches, deformations, cracks and other problems. Use professional tools to measure the dimensional accuracy and fit clearance of key components, such as the cylindrical error of the unwind shaft and the elastic deformation degree of the tension sensor. According to the wear limit standard provided by the equipment manufacturer, replace the components that exceed the wear limit in time. At the same time, check the tightness of the connection parts of key components to ensure that all bolts and nuts are firmly and reliably connected to prevent loosening and causing component displacement or damage. Regular inspection of the wear of key components can effectively prevent sudden equipment failures, reduce equipment maintenance costs, and ensure the continuity of the production process and the stability of product quality.
Transmission system lubrication and maintenance: The transmission system of the equipment includes many gears, chains, bearings, guide rails and other components, and their lubrication conditions directly affect the smooth operation and service life of the equipment. The transmission system needs to be fully lubricated and maintained every month. First, refer to the equipment lubrication chart to determine the location of each lubrication point and the type of lubricant used. For gears and chains, use special gear oil or chain lubricant, and use an oil gun or brush to evenly apply an appropriate amount of lubricant to the gear tooth surface and the chain links of the chain to ensure that the oil film covers the entire surface and reduce the friction and wear of the gears and chains during operation. For bearings and guide rails, use high-temperature, high-load performance grease, and use a grease gun to inject the grease into the lubrication nozzles of the bearing seat and guide rails until the old grease is completely squeezed out by the new grease. During the lubrication process, pay attention to the operation of the transmission parts. If there is abnormal noise or jamming, stop the machine immediately for inspection and troubleshooting. Good lubrication and maintenance can increase the transmission efficiency of the equipment by 20% - 30%, effectively reduce the energy consumption and maintenance frequency of the equipment, and ensure the long-term stable operation of the equipment.
Sensor and control system calibration: The normal operation of the automatic sanitary napkin machine depends on the precise coordination of various sensors and control systems. The sensors and control systems need to be calibrated and adjusted once a month. First, use standard calibration tools and instruments, such as high-precision tension meters, displacement sensor calibrators, etc., to calibrate key sensors such as tension sensors, position sensors, and speed sensors. According to the calibration procedure provided by the equipment manufacturer, gradually adjust the parameter settings of the sensor to ensure that the error between its measured value and the actual value is controlled within the allowable range, and the error is generally required to be no more than ±1%. For intelligent control systems, it is necessary to regularly update the software program and optimize the control algorithm to adapt to changes in material properties and process requirements during the production process. At the same time, the operation interface of the control system is comprehensively inspected and tested to ensure that each button and touch screen area responds sensitively and the displayed data is accurate. Calibration and adjustment of sensors and control systems can effectively improve the production accuracy and automation level of the equipment, reduce the production of defective products caused by sensor drift or control system errors, and ensure product quality and production efficiency.
SAP metering device accuracy maintenance: The accuracy of the SAP metering device is one of the core factors to ensure the quality of sanitary products. The SAP metering device needs to be accurately maintained once a week. First, use high-precision metering tools, such as electronic balances, flow meters, etc., to actually measure and calibrate the powder amount of the SAP metering device. Under different production speeds and SAP application amount settings, collect multiple sets of data to analyze the deviation between the actual output value of the metering device and the set value. According to the measurement results, fine-tune the parameters of the metering device, such as adjusting the speed of the metering screw, changing the supply pressure of the SAP powder, etc., until the deviation between the actual output value and the set value is controlled within ±2.5%. At the same time, check the vulnerable parts of the metering device, such as the screw, hopper, valve, etc. If there is wear or blockage, repair or replace them in time. Maintaining the accuracy of the SAP metering device can effectively ensure the uniformity of the product's gram weight and the consistency of its absorption performance, reduce the waste of raw materials, and improve the market competitiveness of the product.
Seasonal maintenance and storage: During the season change period, the equipment needs to be fully maintained in a seasonal manner to adapt to changes in environmental conditions. First, the equipment is thoroughly cleaned and rust-free, especially the external metal surface and moisture-prone parts of the equipment. Use a professional rust remover to apply to the rusted parts, wait for it to fully react, wipe it clean with a clean cloth, and then apply a thin layer of anti-rust oil to prevent the equipment from rusting and corroding during the season change process. Secondly, check the electrical system and insulation measures of the equipment to ensure that the equipment can operate normally under extreme weather conditions (such as high temperature, severe cold, humidity, etc.). For equipment that is not used for a long time, it should be stored in a dry, ventilated environment without corrosive gases, and the key components of the equipment should be wrapped and protected to prevent dust and external environment from damaging them. At the same time, the equipment should be powered on for a short test run regularly (at least once a month) to check whether the various functions of the equipment are normal, so as to avoid aging or failure of components caused by long-term idleness of the equipment. Seasonal maintenance and storage can effectively extend the service life of the equipment, ensure that the equipment always maintains good performance and reliability in different seasons and use cycles, and provide strong guarantee for the stable production of the enterprise.
Foshan Saibang Intelligent Equipmemt Co., Ltd. is located in nanhai District, an important industrial town in Guangdong Province, is a research and development, manufacturing, sales in one of the National High-tech Enterprise. The founding team of the company has been deeply engaged in the new material industry for 15 years, and is committed to the R&D, manufacturing and technical integration of special equipment for the new material & medical and eisai special equipment, providing systematic solutions and technical services for customers. We have over 30 independent intellectual property rights, and after years of experience accumulation, we currently has customers all over the country, Southeast Asia, Europe, and South America.Our products include casting/laminating equipment, coating machine, non-woven special equipment, all kinds of non-standard automation equipment and related mechanical and electrical accessories.
We adhere to the development philosophy of "technology leading, quality winning, service first, and win-win cooperation", with continuous research and development power for the industry to push technical equipment of cutting edge, with stable quality based on competitive global market, with sincere technology service realize the value of customer demand.