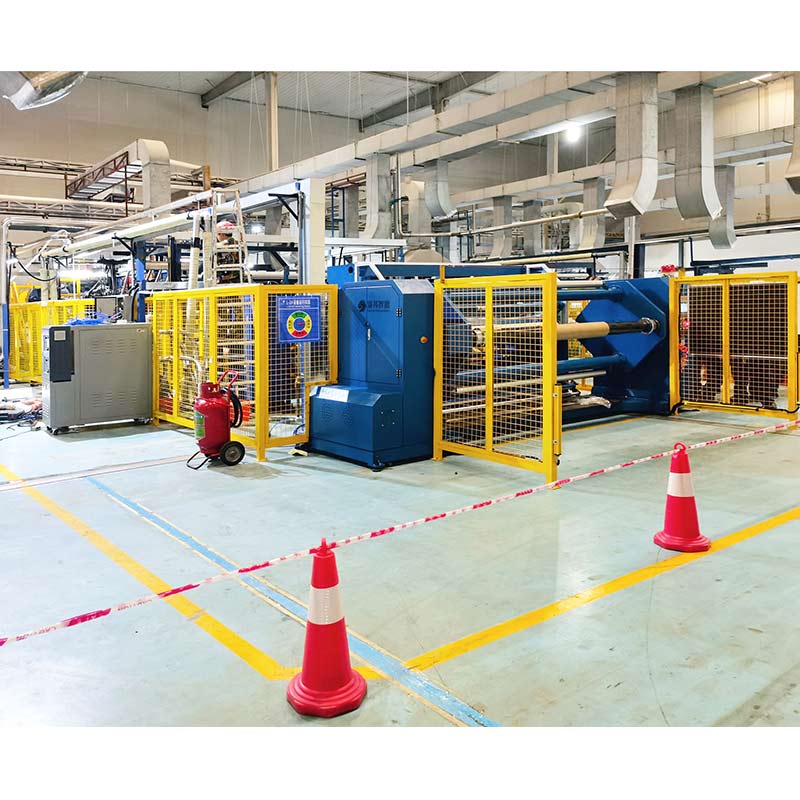
Cast Film Extruder is a high-performance, multifunctional production equipment used to manufacture a variety of materials such as high-strength lithium battery separators, breathable films, wrapping films, printed films, packaging composite films, and high-temperature cooking films. It can achieve efficient production and meet diverse production needs through advanced slitting systems and low-energy consumption design.
Three Layers Co Extrusion Cast Film Extruder parameter
Model: | SCPE25A |
Brand: | Saibang Intelligence |
Scope Of Application: | Suitable For The Production Of Lithium Battery Film, Breathable Film, Winding Film, Printing Film, Packaging Composite Film, High Temperature Cooking Film And Other Materials., Etc. |
Product Width: | 1200-3500mm |
Product Thickness Range: | 25-500um |
Winding Diameter: | 600-1000mm |
Mechanical Design Speed: | 250m/min |
Features: | The Mold Width Can Be Adjusted To Adapt To Various Specifications; Multiple Slitting Knives Can Be Set To Achieve Online Slitting And Winding. |
OEM: | OEM/ODM |
Factory Nature: | China Manufacturers Suppliers Factory |
Three Layers Co Extrusion Cast Film Extruder features
Low energy consumption design: Cast Film Extruder adopts low energy consumption design, which greatly reduces production costs. Its energy consumption can be reduced by more than 30%, effectively reducing energy consumption. This low energy consumption design not only reduces the operating costs of enterprises, but also helps to protect the environment, reduce carbon emissions, and make enterprises more competitive in green production. Through the optimized heating system and efficient energy management system, the equipment can minimize energy waste while ensuring production efficiency, bringing significant economic benefits to enterprises.
Advanced slitting system: Equipped with an advanced slitting system, it can achieve efficient online slitting and winding operations, and the slitting accuracy can reach ±0.1mm to ensure product quality. The system uses high-precision tools and advanced control systems to accurately divide the film into the required width to meet the needs of products of different specifications. Whether it is a single-layer film or a multi-layer composite film, it can ensure that the slitting edges are neat and smooth, avoid material waste and production interruptions caused by uneven slitting, and effectively improve production efficiency and yield.
Product width range: The product width range is 1200-3500mm, which can adapt to different production needs and meet diversified product specifications. This wide width range enables the equipment to flexibly cope with film production tasks of different sizes. Whether it is a small packaging film or a large industrial film, it can be produced on one device, which greatly improves the versatility and production efficiency of the equipment. By adjusting the mold and the winding device, products of different widths can be quickly switched, reducing equipment adjustment time and line change costs.
Product thickness range: The product thickness range is 25-500um, and a variety of thicknesses can be produced to adapt to different application scenarios. From ultra-thin lithium battery separators to thicker high-temperature cooking films, the equipment can accurately control the film thickness to ensure that the product performance meets specific requirements. Through precise extrusion control and cooling systems, uniform thickness distribution can be achieved, avoiding performance differences caused by uneven thickness, and enhancing the market competitiveness of products.
Large diameter winding: The winding diameter can reach 600-1000mm, which improves production efficiency and reduces the number of roll changes. The large diameter winding device can reel in more materials in a single production, thereby reducing the frequency of roll changes and reducing downtime caused by roll changes. At the same time, large diameter winding can also improve the packaging efficiency of materials, reduce the use of packaging materials, and reduce production costs. Through optimized winding tension control, the film is ensured not to be loose, wrinkled or broken during the winding process, thus ensuring product quality.
Mechanical design speed: The mechanical design speed is as high as 250m/min, which greatly improves production efficiency and meets the needs of high-speed production. This high-speed design enables the equipment to complete large-scale production tasks in a short time and adapt to the requirements of modern industry for efficient production. Through the optimized transmission system and stable operation mechanism, the equipment can still maintain good stability and precision when running at high speed, reduce vibration and wear caused by high speed, and extend the service life of the equipment.
Adjustable mold width: The mold width is adjustable and can adapt to a variety of specifications and flexibly respond to different production tasks. The adjustable design of the mold enables the equipment to quickly adapt to the production needs of different widths, and the switching of products of various specifications can be completed without changing the mold. This design not only saves mold replacement time and cost, but also improves the production flexibility of the equipment, enabling it to better meet the diversified needs of the market.
Multi-knife slitting function: Multiple slitting knives can be set to achieve online slitting and winding, and improve production flexibility. The multi-knife slitting function allows slitting tasks of multiple widths to be completed simultaneously during the production process, reducing subsequent processing steps and improving overall production efficiency. Through precise tool positioning and control, it is possible to achieve simultaneous production of products of various specifications and meet customers' demands for diversified products.
Lithium battery diaphragm production: In the production of lithium battery diaphragms, Cast Film Extruder can produce diaphragm materials with high precision and high strength to meet the strict requirements of the battery industry for diaphragm performance. The equipment ensures the thickness uniformity and porosity consistency of the diaphragm through precise temperature control and extrusion process, thereby improving the performance and safety of the battery. The diaphragms it produces are widely used in electric vehicles, energy storage equipment and other fields, providing key material support for the development of the new energy industry.
Breathable film manufacturing: used for the production of breathable films to ensure that the film materials have good breathability, suitable for medical, health and other fields. The equipment uses a special extrusion process and cooling system to produce a breathable film with a microporous structure, which can effectively block liquid penetration and ensure the free flow of gas. This breathable film is widely used in medical protective clothing, sanitary products and other products, providing reliable protective materials for the medical and health industries.
Stretch film production: produces high-strength stretch film, which is widely used in packaging, logistics and other industries, providing excellent winding performance. Through the optimized extrusion process and winding system, the equipment can produce stretch film with high tensile strength and good adhesion. This kind of wrapping film can tightly wrap the goods during the packaging process, prevent the goods from being damaged during transportation and storage, and improve logistics efficiency and packaging safety.
Printing film manufacturing: manufacture high-quality printing films to meet the printing industry's requirements for high clarity and printing adaptability of film materials. The printing film produced by this equipment has good flatness and surface finish, which can ensure the clarity and color reproduction of the printed pattern. It is widely used in food packaging, advertising and other fields, providing high-quality substrates for the printing industry, and enhancing the visual effects and market competitiveness of products.
Packaging composite film production: used for the manufacture of packaging composite films to ensure that packaging materials have good sealing and durability. Through multi-layer co-extrusion technology, the equipment can produce composite films with multiple functions, such as barrier properties, moisture resistance, high temperature resistance and other properties. This composite film is widely used in food, medicine, electronic products and other fields, providing reliable guarantee for the long-term storage and transportation of products and extending the shelf life of products.
High-temperature cooking film manufacturing: produce high-temperature cooking films, which are suitable for high-temperature cooking packaging in the food processing industry to ensure food safety. The equipment uses special material formulas and extrusion processes to produce cooking films that can maintain stable performance under high temperature conditions. This kind of film material will not release harmful substances during high-temperature cooking and can effectively maintain the nutrition and taste of food. It is widely used in the packaging of meat, canned food and other foods to ensure food safety and quality.
Three Layers Co Extrusion Cast Film Extruder maintenance
Check the transmission system regularly: Check the lubrication of the transmission system regularly to ensure that gears, bearings and other components are well lubricated, reduce wear and extend service life. It is recommended to check the lubricating oil level once per shift and conduct a comprehensive lubrication inspection and replenishment once a week. At the same time, check the tension of the transmission belt to ensure that it is within the specified range to avoid the decrease in transmission efficiency and equipment vibration caused by belt relaxation. Through regular maintenance, transmission system failures can be effectively prevented to ensure the stable operation of the equipment.
Clean the surface of the equipment: Clean the surface of the equipment regularly to remove dust, oil and other impurities, keep the equipment clean and tidy, and prevent impurities from affecting product quality. After the end of production every day, the surface of the equipment should be wiped with a clean rag, especially paying attention to cleaning key parts such as the extruder head, mold and winding device. For oil stains that are difficult to clean, special detergents can be used for cleaning, but it is necessary to ensure that the detergent does not corrode the surface of the equipment. Regular cleaning can not only increase the service life of the equipment, but also ensure the hygiene of the production environment and guarantee product quality.
Check the electrical system: Check the connection of the electrical system regularly to ensure that the wires and cables are not aging or damaged to prevent electrical failures. Conduct a comprehensive inspection of the electrical system once a month, focusing on whether the wire connectors are loose and whether the insulation layer is damaged. At the same time, test the performance of electrical components, such as relays and contactors, to ensure that they are flexible and reliable. Through regular electrical inspection and maintenance, electrical fires and equipment failures can be effectively prevented, and production safety can be guaranteed.
Maintain the slitting system: Regularly maintain the slitting system, check the sharpness and installation accuracy of the tool, and ensure the slitting quality. It is recommended to conduct a comprehensive inspection and grinding of the slitting tool after every 1,000 tons of product production to ensure that the blade is sharp. At the same time, check the installation position and tightening of the tool to ensure the stability of the tool during the slitting process. By regularly maintaining the slitting system, slitting quality problems caused by tool wear or improper installation can be effectively avoided, and the product yield rate can be improved.
Check the winding device: Regularly check the operation of the winding device to ensure that the winding tension is stable and prevent the film from winding unevenly. Before production every day, the surface cleanliness and smoothness of the winding roller should be checked to ensure that the film is not scratched during the winding process. At the same time, test the winding tension control system to ensure that it can automatically adjust the tension under different winding diameters to maintain the neatness and tightness of the film winding. By regularly checking and adjusting the winding device, the packaging quality and storage stability of the product can be effectively improved.
Replace wearing parts: timely replace wearing parts such as seals, filters, etc. to ensure the normal operation of the equipment and avoid production interruptions due to component damage. It is recommended to check the seals of the equipment once a quarter, and replace aging or damaged seals in time to prevent oil leakage, material leakage and other problems caused by poor sealing. At the same time, regularly replace the filter to ensure the smooth flow of the material conveying system and avoid production failures caused by impurities. By replacing wearing parts in time, the service life of the equipment can be effectively extended and maintenance costs can be reduced.
Calibrate the mold: Regularly calibrate the mold to ensure the accuracy of the mold width and thickness to meet the production needs of different products. After producing 500 tons of products, the mold should be fully calibrated to check the dimensional accuracy and surface finish of the mold. Adjust the width and thickness parameters of the mold through professional calibration tools and equipment to ensure that it meets production requirements. Regularly calibrating molds can not only improve product quality, but also extend the service life of molds and reduce production costs.
Train operators: Regularly train operators to improve their operating skills and maintenance awareness to ensure the correct use and maintenance of equipment. Operator training is organized every six months, including equipment operating procedures, daily maintenance methods, common troubleshooting, etc. Through practical operation drills and theoretical knowledge explanations, operators can master the use and maintenance skills of equipment. Improving the skill level and maintenance awareness of operators can not only reduce equipment failures caused by misoperation, but also improve the operating efficiency and production quality of equipment.
Foshan Saibang Intelligent Equipmemt Co., Ltd. is located in nanhai District, an important industrial town in Guangdong Province, is a research and development, manufacturing, sales in one of the National High-tech Enterprise. The founding team of the company has been deeply engaged in the new material industry for 15 years, and is committed to the R&D, manufacturing and technical integration of special equipment for the new material & medical and eisai special equipment, providing systematic solutions and technical services for customers. We have over 30 independent intellectual property rights, and after years of experience accumulation, we currently has customers all over the country, Southeast Asia, Europe, and South America.Our products include casting/laminating equipment, coating machine, non-woven special equipment, all kinds of non-standard automation equipment and related mechanical and electrical accessories.
We adhere to the development philosophy of "technology leading, quality winning, service first, and win-win cooperation", with continuous research and development power for the industry to push technical equipment of cutting edge, with stable quality based on competitive global market, with sincere technology service realize the value of customer demand.